ThermaThal® Ceramic Fiber Heater: Understanding the Classification of Heating Alloys
As a crucial component in ceramic fiber heaters, heating alloys play a significant role in ensuring optimal performance. But what sets these heating alloys apart? This article delves into the detailed classification of heating alloys within ThermaThal® ceramic fiber heater.
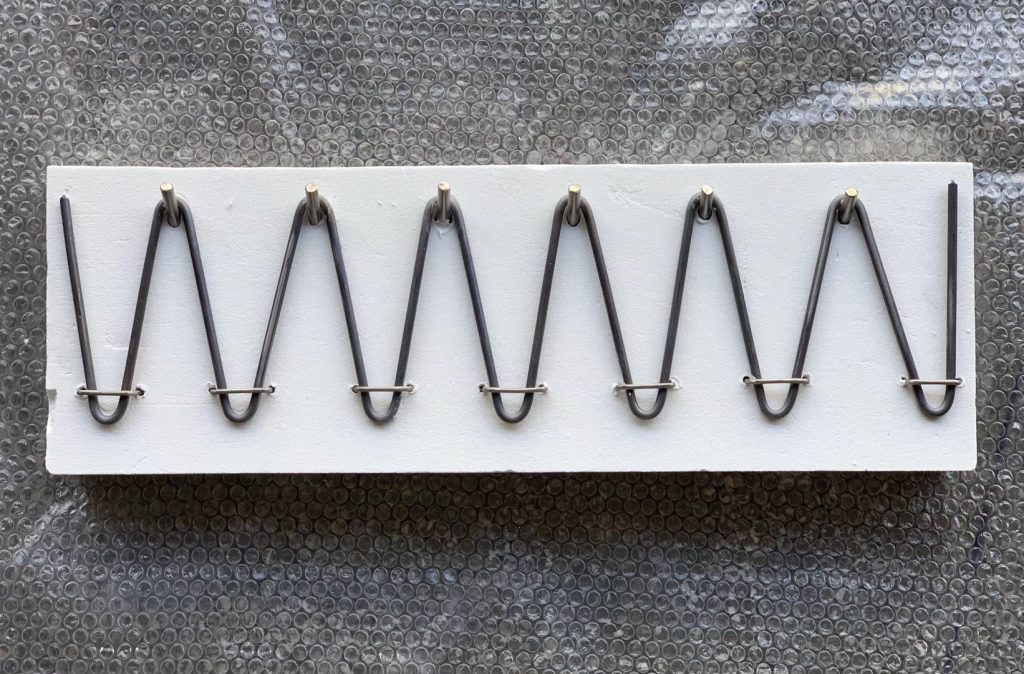
Which Heating Alloys Are Most Commonly Used in Ceramic Fiber Heaters?
When it comes to ceramic fiber heaters, two types of heating alloys are widely utilized – Iron-Chromium-Aluminum (FeCrAl) and Nickel-Chromium (NiCr) alloys.
1.FeCrAl alloys are known for their high resistivity and ability to withstand high surface loads. They can be used at element temperatures as high as 1425°C (2600°F). On the other hand, NiCr alloys exhibit excellent thermal mechanical properties, along with good oxidation and corrosion resistance. They can operate at element temperatures up to 1250°C (2282°F). It’s important to note that these temperatures are achievable in open-wound element configurations. In spiral-wound resistor wire heaters. the furnace temperature should be lower than the maximum element temperature, with FeCrAl at 1200°C (2192°F) and NiCr at 1000°C (1832°F).
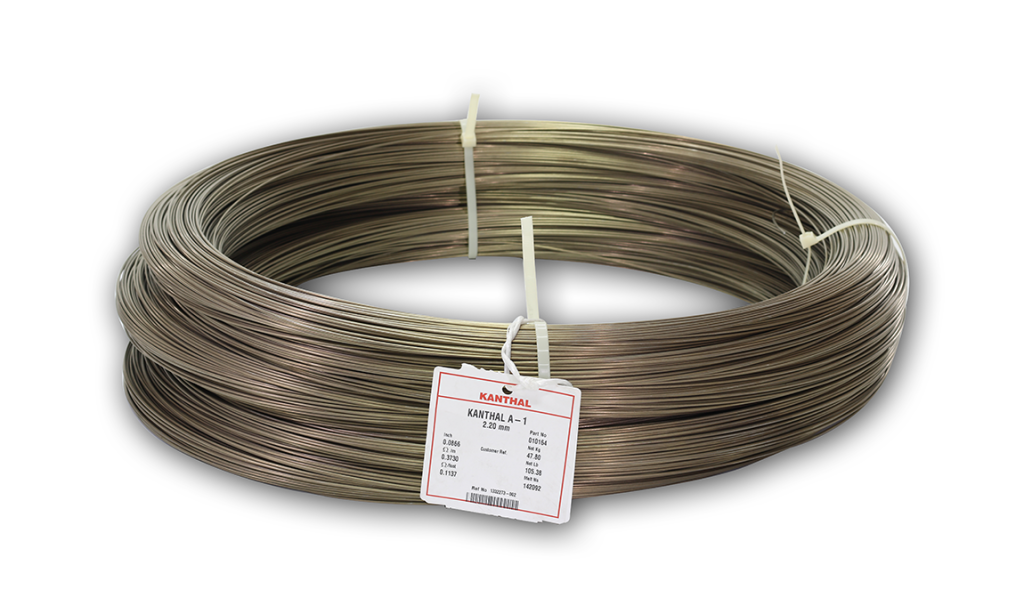
Distinguishing Based on Operating Environments:
For heating environments exposed to air (without a sheath) or containing corrosive gases, it’s generally recommended to use NiCr materials.
Extensive Application in Various Industries:
These heating alloys find wide applications in experimental furnaces, industrial ovens, powder metallurgy, oil pipelines, photovoltaic semiconductor industry high-temperature thermal processing equipment, and more.
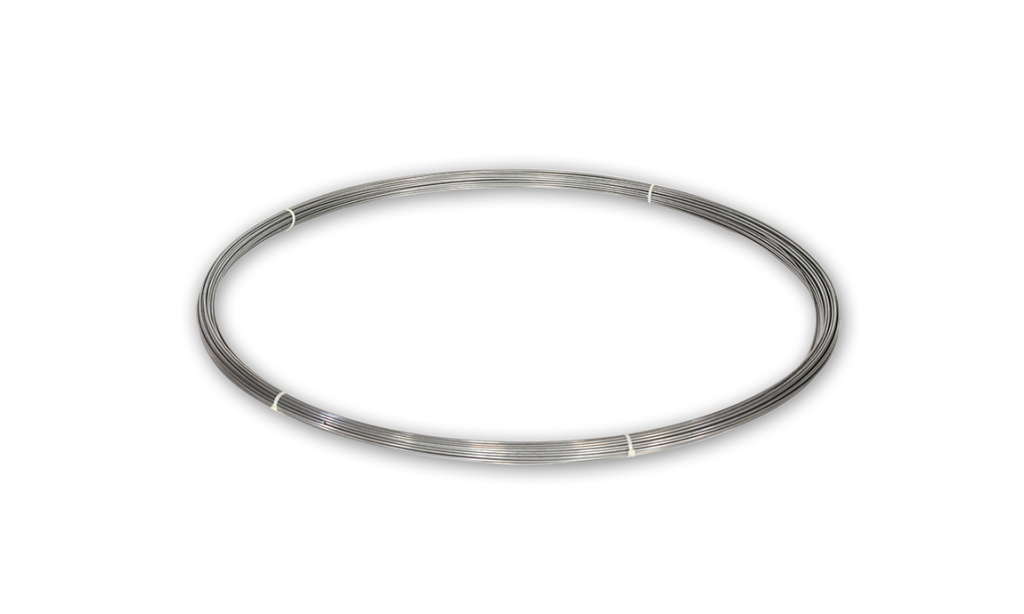
Distinguishing by Alloy Costs:
Due to the presence of precious metals like nickel and chromium in NiCr alloys .they are priced higher than FeCrAl alloys. However, NiCr alloys offer superior high-temperature strength, corrosion resistance, and longer lifespan.
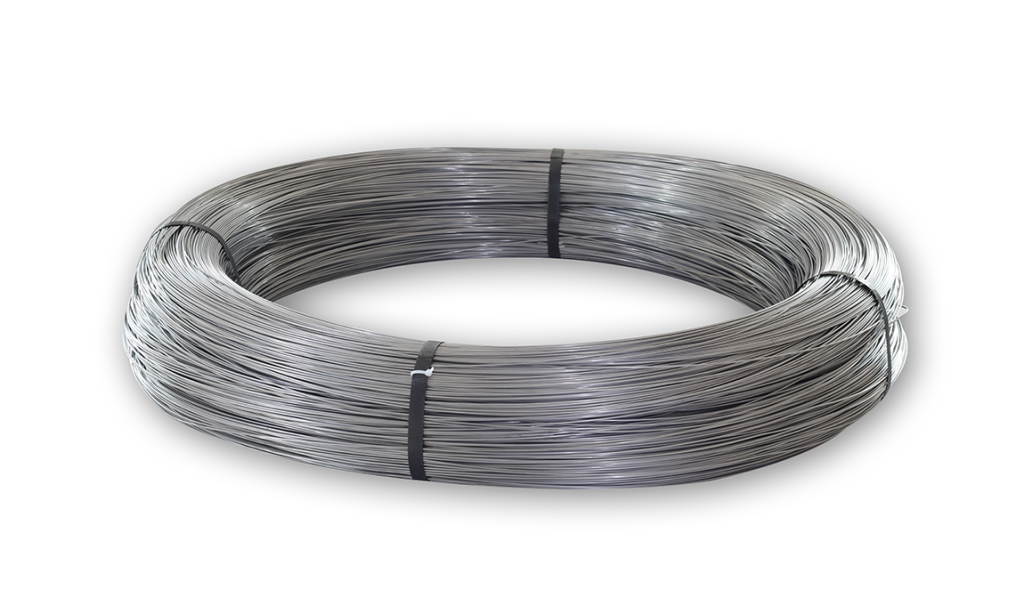
Advantages of ThermalThal® Heating Modules:
ThermalThal® heating modules embed Iron-Chromium-Aluminum (FeCrAl) or Nickel-Chromium (NiCr) alloy wires through vacuum adsorption forming. By securely fixing the resistor wire within refractory fibers. Any deformation due to softening at high temperatures is prevented. thus enhancing the longevity of the resistor wire.
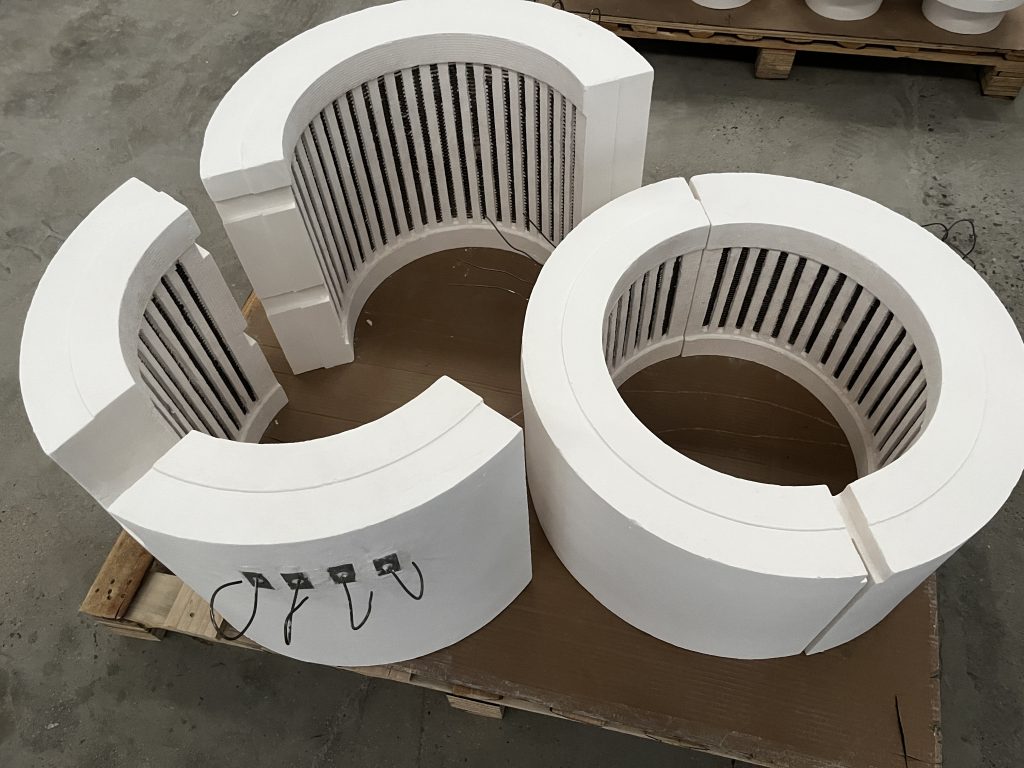
With exceptional high-temperature resistance and fire protection properties. ThermalThal® heating modules are extensively used in various industrial high-temperature equipment, pipelines making them the ideal choice across multiple industries. Whether it’s for insulating equipment in high-temperature environments or protecting critical areas from fire. ThermalThal® heating modules offer reliable solutions to ensure the safety and efficient operation of equipment.
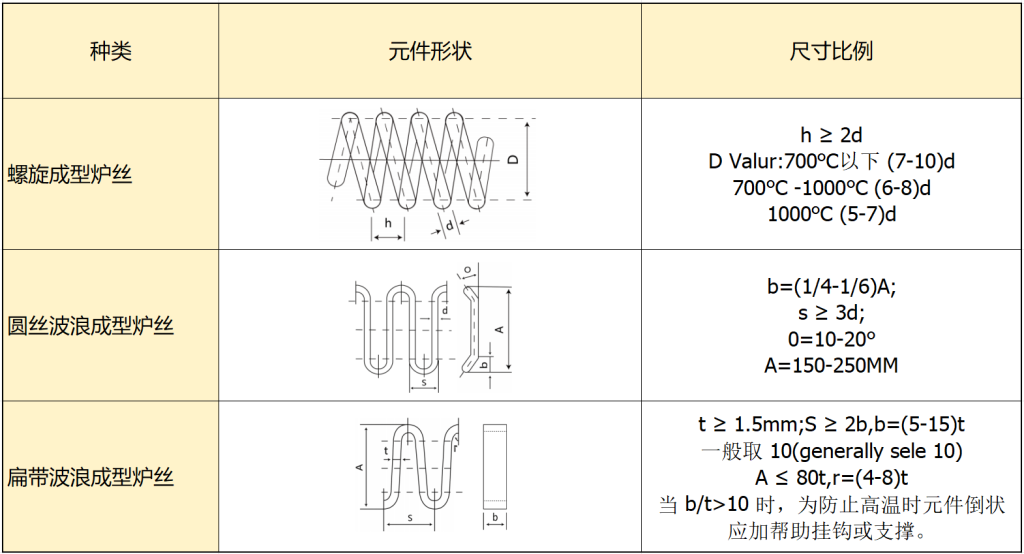