
Introduction
In the chemical industry, enamel equipment sintering furnaces require high thermal efficiency and durability to ensure consistent production quality. Ceramic fiber modules have emerged as a revolutionary lining material for such furnaces, offering exceptional insulation, rapid installation, and resistance to extreme thermal conditions. This article explores the critical advantages of ceramic fiber modules in enamel sintering furnaces, focusing on their unique characteristics and practical benefits for industrial applications.
7 Key Features of Ceramic Fiber Modules
1. Flexible Installation: Parallel and Parquet Types
Ceramic fiber modules support parallel-type and parquet-type installation methods, catering to diverse furnace geometries and thermal requirements.
- Parallel Installation: Modules are aligned horizontally along the furnace walls, ideal for large or cylindrical furnaces, ensuring quick deployment.
- Parquet Installation: Modules are interlocked in a staggered pattern, enhancing structural integrity and minimizing heat leakage.
This adaptability reduces installation time and optimizes furnace performance across complex designs.
2. Superior Elasticity for Gap-Free Sealing
The high elasticity of ceramic fiber modules allows them to compensate for furnace shell expansion during thermal cycles. This eliminates gaps between modules, preventing heat loss and maintaining consistent internal temperatures. Unlike rigid refractory bricks, ceramic fibers adapt dynamically to thermal stress, extending furnace lifespan.
3. Ultra-Low Thermal Conductivity
With a thermal conductivity of 0.08–0.12 W/(m·K) at 800°C, ceramic fiber modules outperform traditional refractory materials. Their porous structure minimizes heat transfer, reducing energy consumption by 20–40% and ensuring uniform temperature distribution for precise enamel sintering processes.
4. Exceptional Thermal Shock Resistance
Ceramic fiber modules withstand rapid temperature fluctuations (up to 1400°C), making them ideal for enamel furnaces that undergo frequent heating-cooling cycles. Their non-brittle nature prevents cracking, even under aggressive thermal stress, ensuring reliable performance in harsh chemical environments.
5. Immediate Use Post-Installation (No Curing Required)
Unlike conventional linings that require lengthy drying and curing, ceramic fiber modules are ready to use immediately after installation. Containing no binders or moisture, they eliminate downtime for烘炉 (drying) and accelerate furnace commissioning.
6. Cold-Side Anchoring System for Enhanced Safety
The anchoring system of ceramic fiber modules is strategically positioned away from the hot face, operating at low temperatures (<300°C). This design prevents anchor oxidation and thermal fatigue, ensuring long-term structural stability and reducing maintenance costs.
7. Versatile Anchoring Solutions
Multiple anchoring systems, such as welded bolts, V-shaped pins, and banding kits, are available to suit specific furnace designs. These options enable secure module fixation while accommodating thermal expansion, vibration, and mechanical loads.
Applications in Chemical Enamel Sintering Furnaces
- Improved Enamel Coating Quality: Uniform insulation minimizes temperature gradients, reducing defects like pinholes or bubbles in enamel products.
- Corrosion Resistance: Ceramic fibers resist acidic gases and chemical vapors common in enamel furnaces, ensuring long-term durability.
- Energy and Cost Savings: Reduced fuel consumption and faster heat-up cycles lower operational expenses by up to 30%.
Case Study: Energy Efficiency Upgrade in a Chemical Plant
A chemical manufacturer replaced traditional refractory bricks with ceramic fiber modules in their enamel sintering furnace, achieving:
- 35% reduction in natural gas consumption;
- 40% faster heat-up time (from ambient to 800°C);
- 60% lower annual maintenance costs due to enhanced anchor system reliability.
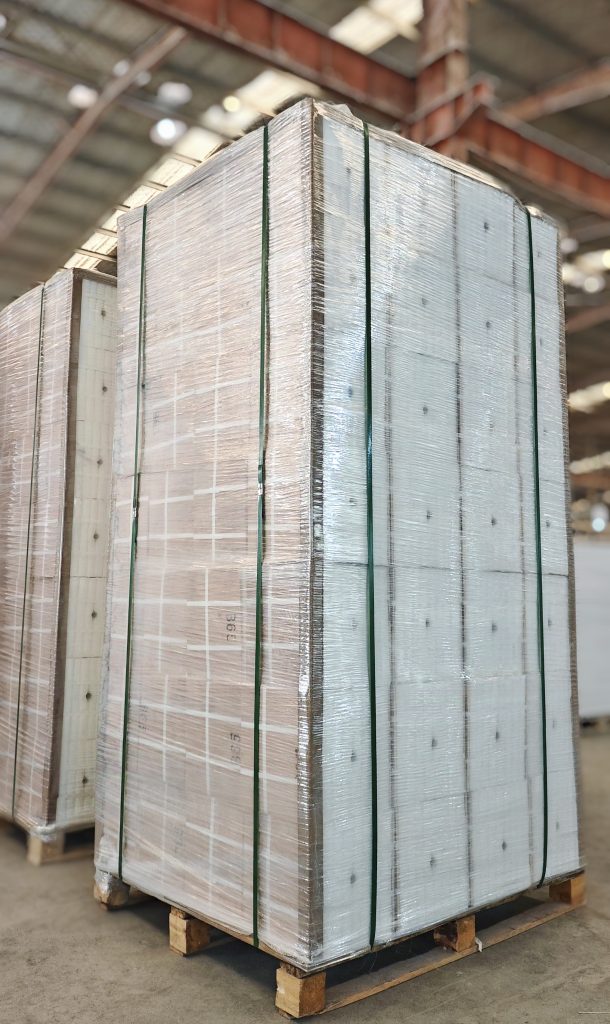